The necessity to reuse waste timber as feedstock for new
laminated timber products
As the saying goes, “money doesn’t grow on trees”. However, unlike money, wood does grow on trees. If forestry resources are well-managed, then the use of timber as a structural material – as opposed to non-renewable energy-intensive materials such as concrete or steel – can reduce the embodied carbon emissions of constructing our built environment.
However, timber construction has the potential to do more. As trees grow, they photosynthesise carbon dioxide from the atmosphere and store it in solid form as sugars in the molecular structure of new materials – a tree’s leaves, stems, bark, trunk, roots, and the soil below it. As trees die, they decompose, and these solid sugars are converted back to carbon dioxide, which is released into the atmosphere. This is the basic carbon cycle of a stable forest. When using timber as a construction material, we remove some of the solid carbon from this stable carbon flow and store it in our buildings, where it is prevented from decomposition or combustion. This reduces the total carbon dioxide in our atmosphere. This reduction is our primary goal when attempting to mitigate further climate change.
For carbon storage in structural timber to have a long-term mitigation effect on climate change, we must prevent timber from releasing its solid carbon back into the atmosphere as carbon dioxide at the end of a structure’s life. The most effective way to prevent this release is to keep the timber encapsulated in the primary frame of a structure for as long as possible, through continued use, refurbishment, or adaptive reuse of a structure. Unfortunately, as another saying goes, “all good things must come to an end”. No structure is permanent; whether surviving for 40 years or 400, all structures will eventually be demolished. The demolition of buildings produces waste timber. In Germany 20 % of waste wood is recycled to manufacture particle board and 80 % is incinerated for energy. In the USA 17 % of waste wood is recycled, 16 % is incinerated for energy, and 67 % is sent to landfill. In most circumstances these processes soon release the solid carbon in the timber molecular structure back into the atmosphere. Data on reuse or upcycling – the only waste management practices which effectively prevent carbon being released back into the atmosphere – is not deemed worthy of record.
A market for reusing old growth large-dimension timber exists in the US, particularly in parts of the Northeast region which experienced population growth and housing construction in the second half of the 19th century, and the post-industrial Rust Belt area around the Great Lakes. This wood is hard, dimensionally stable, and aesthetically interesting, but is often diverted to non-structural shorter-life uses such as flooring, cladding and furniture, instead of longer-life uses such as primary structural frames. In the USA, the timber waste stream is dominated by farmed fast-grown small-dimension timber from light-frame construction and non-structural carpentry.
Why do we not reuse more timber? This question is economically pertinent with current structural timber material costs increasing significantly, and debates over supply and demand mismatches for new timber products. This question is primarily environmentally pertinent, as reusing timber has been found to have a third of the global warming potential of new timber. There are existing procedural barriers to easily reusing waste timber structurally: buildings should be deconstructed instead of demolished to maintain maximum salvaged timber lengths and section integrity; salvaged timber material may be damaged or notched; the history, species and material properties of the salvaged timber may be unknown; removing any existing metallic fasteners, such as screws or nails, is currently slow manual labour. We describe these as procedural barriers, as they are not fundamentally serious. They require adjustments to existing demolition and construction practices, but these adjustments are not drastic. If we are to gain the additional short-term economic and long-term environmental benefits of reusing timber, then the construction industry must overcome these barriers.
The market for mass timber products, such as cross-laminated timber (CLT), is growing rapidly, leading to supply shortages and high material costs in the timber industry. Fortunately, recent research studies have successfully demonstrated the feasibility of reusing salvaged timber as feedstock for laminated timber products such as glulam or cross-laminated timber (CLT), where finger jointing of elements and the averaging effects of creating large members from smaller components reduce the impact of many of the existing barriers such as short lengths, small dimensions, localised defects etc. This research is being trialled as a commercial product in the UK and the USA by combining salvaged timber either throughout all laminations, or only in the less-structurally-utilised central laminations for glulam beams, or transverse laminations in CLT panels.
As the saying goes, “the best way to learn is to do”. The goal of the research I have been involved with – as part of the Circular Construction in Regenerative Cities (CIRCuIT) collaborative project funded by the EU’s Horizon 2020 programme – is to better understand the challenges and opportunities of using salvaged timber as feedstock for laminated timber products through completing the deconstruction, processing, and manufacturing process in practice. The project recently coordinated the deconstruction of a raised timber floor from a Central London office building refurbishment and tested the structural strength of six glulam beams fabricated commercially from these salvaged elements. By documenting the process of transporting, storing, denailing, measuring, photographing, and testing these elements, we learnt about the potential to overcome existing labour and equipment barriers for characterising a population of salvaged timber; by transporting the material to a local glulam manufacturer to dry, finger joint, glue and laminate, we learnt about the possibilities of overcoming existing commercial and financial barriers in manufacturing laminated timber products from an imperfect heterogenous source; by transporting the fabricated beams to a university testing facility for stiffness, shear and bending tests, we learnt about the potential of these products to perform satisfactorily as structural elements in future built structures. The barriers to commercial manufacture and use are not yet all resolved, but this work, and other parallel research, continues to develop the viability of laminated timber manufactured with salvaged material as a promising primary structural element with low embodied carbon.
In the world’s current economic and environmental predicament, the construction industry must embrace products and processes which mitigate climate change, such as laminated timber products made from salvaged timber which extend the storage of carbon in the material instead of dispersing it in the atmosphere as carbon dioxide. Salvaging and reusing waste wood in this way requires a change in procedure, but it is no paradigm shift. Even if it is perceived as a major shift, as the saying goes, “fortune favours the brave”.
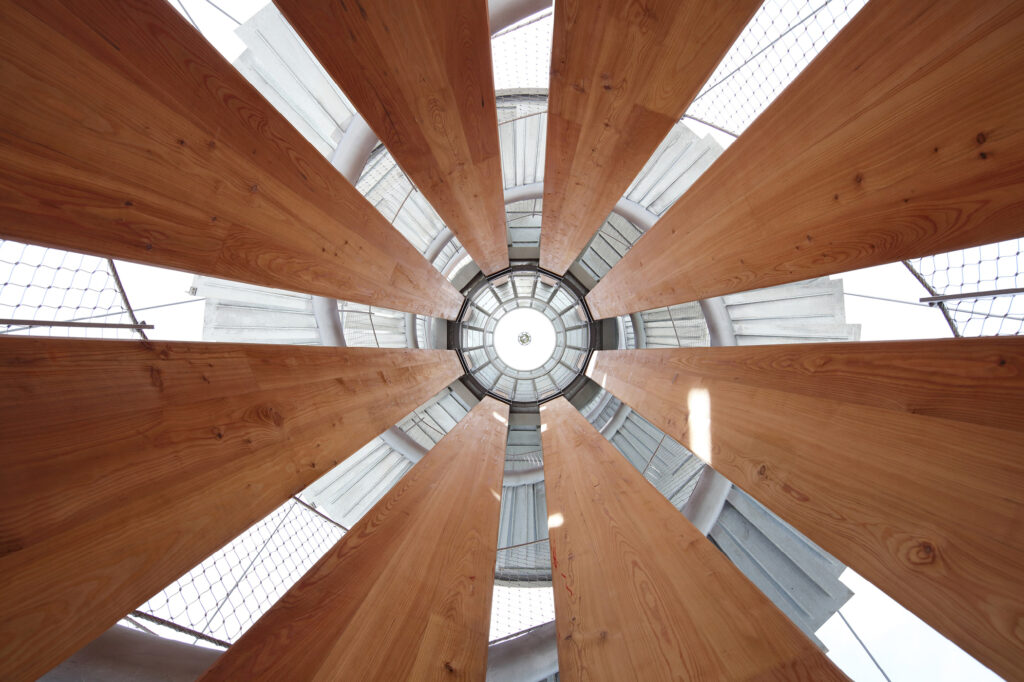
Quelle: Conné van d’Grachten
Authors
Michael Stein, m.stein@sbp.de
Dan Bergsagel, d.bergsagel@sbp.de
schlaich bergermann partner New York